When it comes to warehousing and distribution, efficiency and flexibility are key. That’s why metal buildings—especially those engineered from steel—are becoming the go-to solution for logistics companies looking to expand or upgrade their facilities. Whether you’re planning a regional distribution hub or a specialized storage facility, steel buildings offer unmatched customization to meet your specific operational needs.
Why Choose Metal Buildings for Warehousing?
Modern warehouse metal buildings are far from one-size-fits-all. These structures are engineered with versatility in mind, allowing for scalable designs and tailored functionality to support your logistics operations. With scalable design options, you can easily expand your facility as your business grows, adding extra bays, taller clearances, or even entire wings without significant disruption to operations. Tailored functionality means that metal buildings can be customized with specialized features such as reinforced flooring for heavy equipment, climate control systems for sensitive inventory, or integrated loading docks designed to streamline shipping and receiving. In contrast to traditional construction methods, which often involve lengthy timelines, costly design changes, and structural limitations, metal buildings offer faster build times, lower maintenance costs, and greater flexibility for future modifications. Their structural durability combined with the ability to quickly adapt to changing business needs provides long-term value that traditional methods often can’t match.
Below, we’ll talk about a few ways steel storage buildings can be customized to optimize warehousing and distribution.
1. Space Optimization
Warehousing is all about maximizing usable square footage—and metal buildings make it easy. With clear-span framing, you eliminate the need for interior columns, allowing for wide-open floor plans that are ideal for racking systems, bulk storage, manufacturing equipment, or flexible workstations. This open space can be tailored precisely to your inventory flow, production lines, or employee work zones, reducing bottlenecks and improving overall operational efficiency. Plus, the ability to easily reconfigure floor layouts as business needs change ensures long-term functionality without costly renovations.
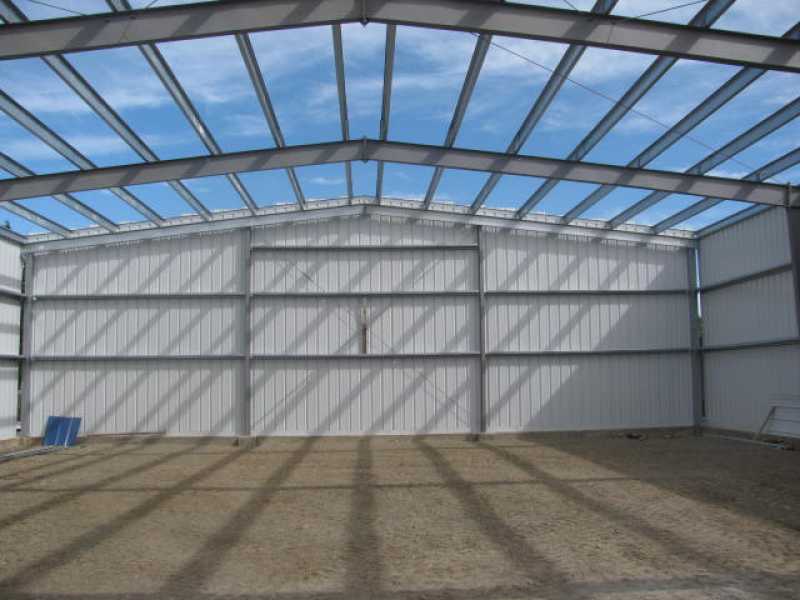
2. High Ceilings for Vertical Storage
Many logistics facilities are moving upward to save on rising land costs and maximize warehouse volume. Steel buildings can be easily designed with high ceilings—30 feet, 40 feet, or more—to accommodate mezzanines, multi-level shelving systems, or advanced automated storage and retrieval systems (ASRS). By taking advantage of vertical space, operations that handle high volumes of palletized goods, oversized inventory, or large equipment can significantly increase storage density without expanding their footprint. This vertical scalability not only saves money but also positions facilities for future technological upgrades.
3. Integrated Loading Docks and Bay Doors
Customizing your warehouse metal building to include loading docks, drive-in doors, or side-access bays can dramatically streamline inbound and outbound freight operations. Whether your business requires dock-high loading for tractor-trailers, at-grade access for small delivery vehicles, or oversized doors for heavy equipment, metal buildings offer the flexibility to design for your exact logistical needs. Strategic placement of these features improves traffic flow, reduces loading and unloading times, and ultimately helps keep your supply chain running efficiently. Our team will work with you to create the functionality that meets your business’s needs.
4. Energy-Efficient Insulation and Ventilation
Keeping your goods—and your staff—at the right temperature is essential for safety, productivity, and cost control. Steel structures can be fitted with high-performance insulation packages, reflective energy-efficient roofing materials, and modern ventilation systems that maintain consistent indoor climates while reducing energy consumption. Options like ridge vents, louvers, and solar-powered exhaust fans help optimize airflow. These features are particularly important for operations in regions with extreme heat, cold, or humidity, or for businesses storing temperature-sensitive products like electronics, pharmaceuticals, or food goods.
5. Adaptability for Future Growth
The modular nature of steel buildings makes planning for future growth not just possible—but easy and cost-effective. Expansion bays, pre-engineered connections, and panelized construction allow for fast additions of extra square footage, new loading docks, warehouse offices, or specialized zones such as cold storage or assembly areas. Because the framework is already designed for flexibility, future modifications require less time and fewer resources compared to traditional buildings. This built-in adaptability means your facility can evolve with your business, protecting your investment and keeping pace with changing market demands.
Build Your Logistics Facility with Allied Steel Buildings
At Allied Steel Buildings, we’ve helped hundreds of businesses across industries design and build custom metal buildings that meet their warehousing and distribution needs. You can see examples of some of our completed projects, such as this steel warehouse in Steelsboro, Georgia or this flex warehouse space in Lakewood, NJ. As you’ll see in these featured projects, from layout planning to final delivery, we’ll work with you to ensure your facility is efficient, durable, and built for your unique logistics operations.
Ready to take the next step? Contact us today to start designing your warehouse or distribution center.